SINTX’s New BoroShock – Boron Carbide
- SINTX
- Jan 26, 2022
- 3 min read
Updated: Jun 17, 2024
Starting in 2022, SINTX is manufacturing and continuing to develop BoroShock, bringing a new level of quality control and expanded product offerings. The SINTX BoroShock material is rather unique in that it is essentially 100% boron carbide that has been densified by pressureless sintering. Typically, boron carbide is hot pressed, which can be very expensive, or it can be produced by reaction bonding which can lead to lower properties due to the metal phase. SINTX believes we have developed a material with right balance between performance and cost.
We are extremely excited about the new material given that it can be used in a variety of applications where its properties offer superior performance. Some examples include:
Personal and vehicle anti-ballistic armor: B₄C is one of the best solutions for high level ballistic armor performance, which requires high hardness and low density.
Grit blasting and high-pressure water jet cutter nozzles: B₄C is commonly used in these demanding applications thanks to its inherent resistance to abrasion and erosion. Neutron absorber in nuclear reactors: The ability of boron carbide to absorb neutrons without forming long-lived radionuclides makes it attractive as an absorbent for neutron radiation arising in nuclear power plants[1]. Nuclear applications of boron carbide include shielding, control rods, and shutdown pellets. Within control rods, boron carbide is often powdered to increase its surface area. In brake linings of vehicles: With its high hardness and wear resistance, boron carbide is a major additive to brake linings in high performance applications.
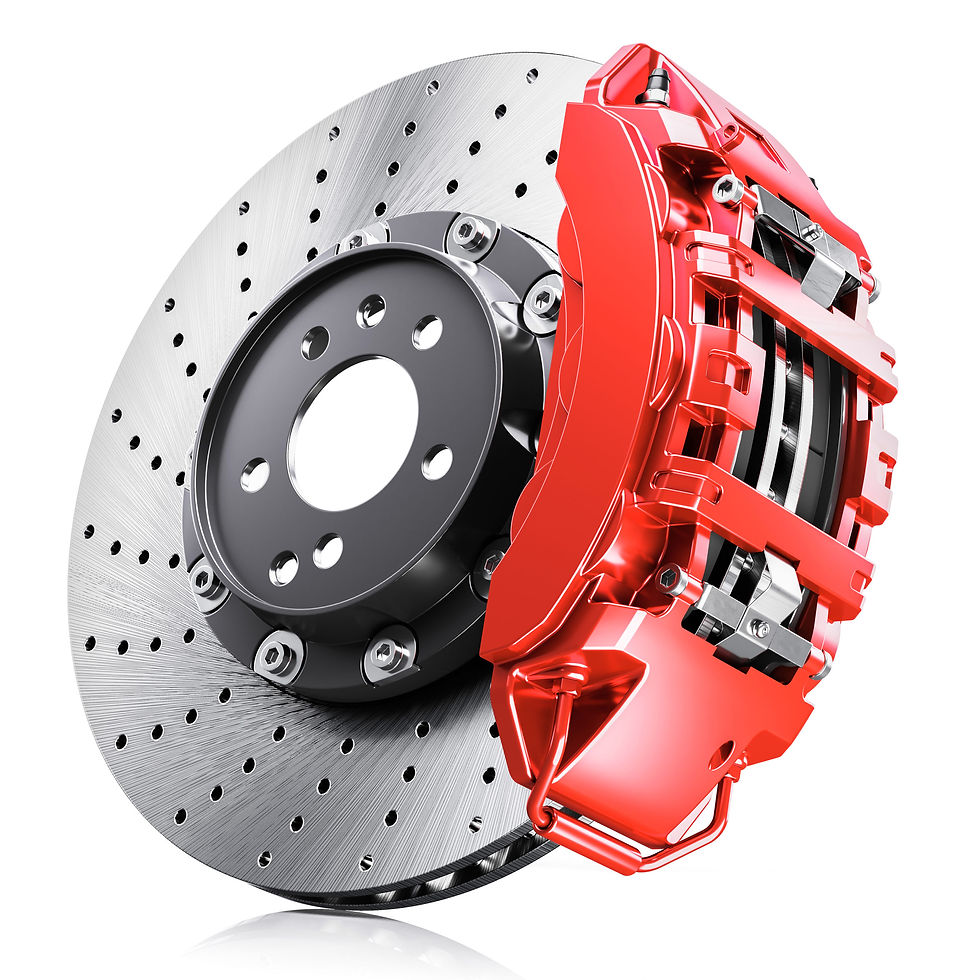
Metal matrix composites: B₄C is added to aluminum alloys to manufacture modern high-performance metal matrix composites with improved strength, thermal behavior, chemical inertness, and wear resistance. High energy fuel for solid fuel ramjets: highly loaded boron carbide combined with Hydroxyl-terminated polybutadiene fuel grains is used in solid-fuel ramjet motors. Please contact us with your applications needing high performance solutions. What are carbides? How are they made? Carbides are compounds composed of carbon and less electronegative elements and are distinguished by their chemical bonding (ionic, covalent). They are generally prepared from metals or metal oxides at high temperatures (1500 °C or higher) by combining the metal with carbon. Interstitial carbides describe the carbides of the group-IV, -V, and VI transition metals. These carbides are ceramic and very refractory. They are formed so that the carbon atoms fit into octahedral interstices in a close-packed metal lattice[2]. Carbides are used in key industrial applications. Boron carbide (chemical formula approximately B₄C) is the lightest of the carbides and is an extremely hard boron–carbon ceramic due to its covalent bonding. With a Vickers hardness of >30 GPa, it is one of the hardest known materials, behind cubic boron nitride and diamond[3]. Boron carbide was first synthesized by Henri Moissan in 1899[4], by reduction of boron trioxide either with carbon or magnesium in presence of carbon in an electric arc furnace. In the case of carbon, the reaction occurs at temperatures above the melting point of B₄C and is accompanied by liberation of large amount of carbon monoxide:[5] 2 B₂O₃+ 7 C → B₄C + 6 CO Boron carbide is known as a robust material having extremely high hardness, high cross section for absorption of neutrons (i.e., good shielding properties against neutrons), stability to ionizing radiation and resistant to most chemicals. It is strong, stiff and lightweight. Its Vickers hardness (38 GPa), Elastic Modulus (460 GPa)[6] and fracture toughness (3.5 MPa·m ¹/²) approach the corresponding values for diamond (1150 GPa and 5.3 MPa·m¹/²).[7]

Figure 1. Unit cell of B₄C. The green sphere and icosahedra consist of boron atoms, and black speres are carbon atoms. [8]
References:
<1> Fabrication and Evaluation of Urania-Alumina Fuel Elements and Boron Carbide Burnable Poison Elements, Wisnyi, L. G. and Taylor, K.M., in "ASTM Special Technical Publication No. 276: Materials in Nuclear Applications", Committee E-10 Staff, American Society for Testing Materials, 1959 <2> Kunst, Helmut; Haase, Brigitte; Malloy, James C.; Wittel, Klaus; Nestler, Montia C.; Nicoll, Andrew R.; Erning, Ulrich; Rauscher, Gerhard (2006). "Metals, Surface Treatment". Ullmann's Encyclopedia of Industrial Chemistry. Weinheim: Wiley-VCH. doi:10.1002/14356007.a16_403.pub2
<3> "Rutgers working on body armor". Asbury Park Press. Asbury Park, N.J. August 11, 2012. Retrieved 2012-08-12. <4> Greenwood, Norman N.; Earnshaw, Alan (1997). Chemistry of the Elements (2nd ed.). Butterworth-Heinemann. p. 149. ISBN 978-0-08-037941-8. <5> Alan W. Weimer (1997). Carbide, Nitride and Boride Materials Synthesis and Processing. Chapman & Hall (London, New York). ISBN 0-412-54060-6. <6> Sairam, K.; Sonber, J.K.; Murthy, T.S.R.Ch.; Subramanian, C.; Hubli, R.C.; Suri, A.K. (2012). "Development of B₄C-HfB2 composites by reaction hot pressing". Int.J. Ref. Met. Hard Mater. 35: 32–40. doi:10.1016/j.ijrmhm.2012.03.004. <7> Solozhenko, V. L.; Kurakevych, Oleksandr O.; Le Godec, Yann; Mezouar, Mohamed; Mezouar, Mohamed (2009). "Ultimate Metastable Solubility of Boron in Diamond: Synthesis of Superhard Diamondlike BC5" (PDF). Phys. Rev. Lett. 102 (1): 015506. Bibcode:2009PhRvL.102a5506S. doi:10.1103/PhysRevLett.102.015506. PMID 19257210. <8> Zhang FX, Xu FF, Mori T, Liu QL, Sato A, Tanaka T (2001). "Crystal structure of new rare-earth boron-rich solids: REB28.5C4". J. Alloys Compd. 329 (1–2): 168–172.